A szabadkai Antal Mihály, a jól ismert Antal-öntöde vezetője sikeres villamosmérnökként dolgozott Budapesten, majd egy osztrák mérőeszközgyártó cég kutató részlegén, aztán tizenöt külföldön töltött év után úgy döntött, hazaköltözik. A Miskolci Egyetem kohómérnöki karán végzett tanulmányai után, még nagyobb szintre emelte az itthon hagyott családi vállalkozást. Az Antal-öntödét nagyapja, Antal Mihály alapította meg 1930-ban.
Ez volt akkor az első kisipari méretű, magán vasöntöde Vajdaságban. Eleinte csak öntöttvassal foglalkoztak, majd amikor Mihály édesapja átvette az öntödét, bevezette a színesfém- és műöntést, majd az acélöntést is, a hetvenes éveket követően pedig szobor- és harangöntésbe is belekezdtek. Az öntöde termékpalettája folyamatosan bővült. Az évtizedek alatt felmerülő technológiai váltásokat és újításokat a vezetők akadálytalanul vették, így ma az öntésen kívül, cégen belül tudják elvégezni a modell- és mintalapkészítést, a minőség-ellenőrző mechanikai és kémiai méréseket, a gépi megmunkálást, sőt, mostanra már a 3D nyomtató is a mindennapjaik részét képezi. A műhely 94 éve ugyanazon a helyen található, jelenleg hat munkás dolgozik itt, akik már szinte egy családként alkotnak nap mint nap.
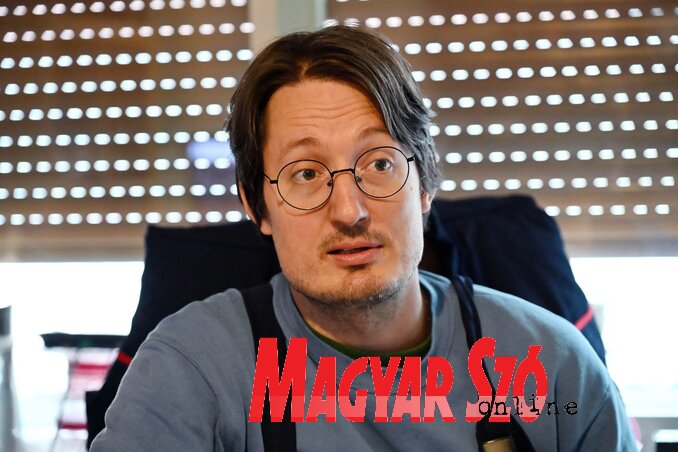
Antal Mihály, az Antal-öntöde vezetője (Fotó: Molnár Edvárd felvétele)
Az ifjabbik Antal Mihállyal az öntöde múltjáról, jelenéről és jövőjéről beszélgettünk. Kitértünk a kezdeti nehézségekre, a fejlesztésekre, és a legszebb alkotásokra is.
Tizenhárom éve vezeti az öntödét. Hogyan emlékszik vissza a kezdetekre, milyen újításokat vitt véghez?
– Miután eldöntöttem, hogy felhagyok a külföldi léttel, kezdetben Magyarországra összpontosítottam volna, de egy merészebb ötlet formálódott bennem: mi lenne, ha az öntödénk nemcsak nyers öntvényeket, hanem készre csomagolt, azonnal használható termékeket kínálna az iparnak? Ez nemcsak a hozzáadott értéket, hanem a szolgáltatásaink színvonalát is növelné. Ehhez azonban bővítésre volt szükség: megdupláztuk a telkünk méretét, új műhelyeket építettünk, és modern, számítógép-vezérelt gépeket – egyebek mellett CNC esztergapadokat, marókat és megmunkáló központokat – szereztünk be, amelyek új szintre emelték a gyártási kapacitást. Olyan termelési profilt alakítottunk ki, amely a 10–15 kilós öntvények kis- és középméretű sorozatgyártására, azok megmunkálására, csomagolására és szükség esetén külföldre szállítására összpontosított. Felfedeztünk egy piaci rést is. Míg a nagy öntödék tízezer darabnál kisebb sorozatok alatt nem vállalnak munkát, a rugalmasságunk és a kis létszámú, de dinamikus csapatunk révén mi akár ötdarabos rendeléseket is teljesítünk, és gyakran már a rendelés hetében leszállítjuk az alkatrészeket. Az ügyfeleink számára nem a darabszám a fontos, hanem a gyorsaság – az alkatrészhiány ugyanis az ő termelésüket állítja meg. Így indult el a prototípusok és cserealkatrészek gyártása, amelyek már nemcsak öntvénykészítést jelentettek, hanem a teljes, beszerelésre kész termék előállítását. Az elmúlt tizenkét évben tehát több lépcsős fejlesztéseket hajtottunk végre, melyek mind a szolgáltatásaink bővítését célozták. Felváltottuk az elavult és szennyező koksz tüzelésű kemencéket korszerű és környezetbarát elektromos indukciós kemencékre. Az öntvények gyártása teljesen ellenőrzött folyamattá vált, a nyersanyagtól kezdve a késztermékig. Minden alkatrészt tanúsítványokkal és mérési jegyzőkönyvekkel szállítunk, így ügyfeleink minőségi termékeket kapnak.
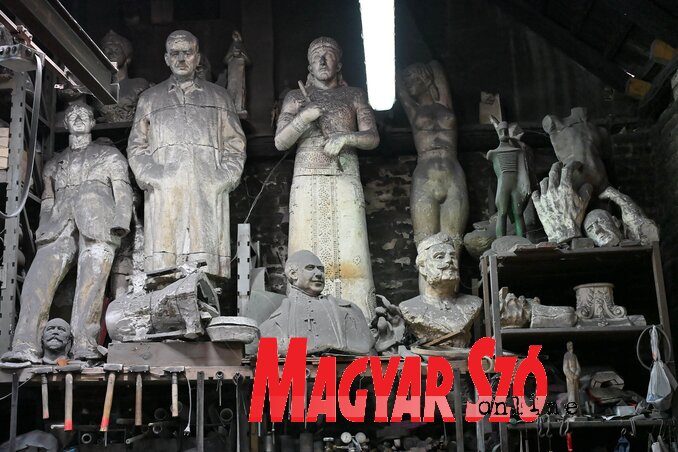
Ezen alkotások az öntödében figyelik nap mint nap az alkalmazottak tevékenységeit (Fotó: Molnár Edvárd felvétele)
Milyen megkereséseik vannak, illetve mit gyártanak?
– Műhelyünkben mindennap izgalmas kihívásokkal találkozunk. Nemcsak azt mérlegeljük, mit vállaljunk el, hanem azt is, mi éri meg. Előfordul, hogy hatalmas szériák gyártására is kapunk megkereséseket, kapacitásunkhoz mérten azonban ezeket nem tudjuk vállalni. A csapatunkat hat munkás, a szüleim és én alkotjuk, így minden projektet okosan kell beosztanunk. A kapcsolattartás szinte teljesen digitális, az ügyfelekkel 99%-ban e-mailben kommunikálunk, és van, akivel személyesen még sosem találkoztunk, mégis évek óta rendszeresen szállítunk neki. Két fő területen működünk: gépalkatrészeket gyártunk, prototípusoktól kezdve kisebb és közepes szériákig, évente akár 2000–5000 darabos mennyiségben, és művészeti projekteket valósítunk meg, például szobrokat, emléktáblákat, domborműveket, maketteket és épületekre szánt feliratokat. Idén különösen izgalmas kihívással találtuk szembe magunkat. A műhely történetének eddigi legnagyobb megbízása a Banja Luka-i monumentális, öt és fél méteres lovas szobor elkészítése volt. Egy évvel korábban Boszniába szállítottuk egy 3 méteres bronz-kompozíciót, amely az első szobor volt, amit 3D-s szkenneléssel és nyomtatással alkottunk meg. Négy éve kezdtünk el 3D-nyomtatókkal dolgozni, ma már hat darab van belőlük. Ennek előnye, hogy az alkotóknak már nem kell agyagban teljesen készre formálniuk a művet, sem eredeti méretben elkészíteni, hiszen mi képesek vagyunk digitálisan nagyítani, kicsinyíteni, vagy éppen részleteket hozzáadni. Míg az első boszniai szobrot egy kisebb 3D-s nyomtatóval készítettük el, idén beruháztunk egy nagyobb, gyorsabb és fejlettebb nyomtatóba, amely egy nap alatt akár 5 kilogramm anyagot is kinyomtat. A Banja Luka-i lovas szobor már ezzel az eszközzel készült, és 3,5 hónapon keresztül szinte megállás nélkül dolgozott, és mintegy 50–60 kilogramm műanyagot használt fel. A projekt a szobor szkennelésével kezdődött, majd a nyomtatás és öntés folyamatosan, párhuzamosan zajlott. Amint egy alkatrész kinyomtatódott, már ment is az öntőműhelybe beágyazásra, majd égetésre, öntésre, csiszolásra, retusálásra, cizellálásra és hegesztésre. Amikor elkészült az alkotás, annak szállítása igazi kaland volt. Csak fektetve lehetett szállítani, speciális járművel és rendőri kísérettel, nagyjából negyven óra alatt ért el a végcélig. A Balkánon egyébként senki sem alkalmaz ilyen innovatív szkennelési, nyomtatási és digitális retusálási technológiát bronzszobrok készítésére. Büszkék vagyunk arra, hogy egyetlen tető alatt képesek voltunk az egész folyamatot végrehajtani.
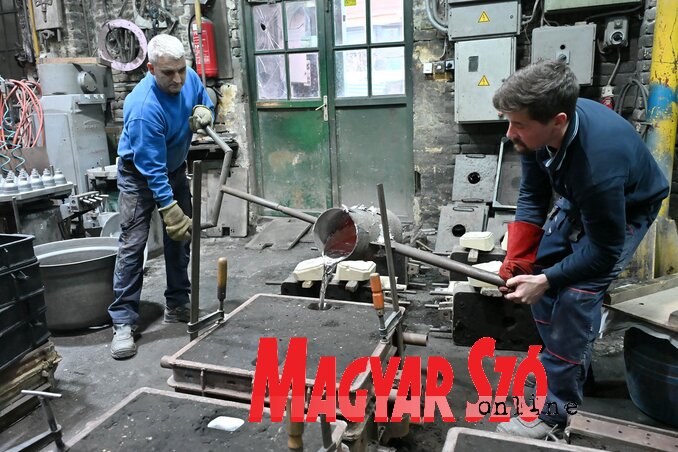
Öntési folyamat közben (Fotó: Molnár Edvárd felvétele)
Sok újítást ön fejlesztett ki, tapasztalati úton.
– Igen. Ezeket az innovációkat jelen pillanatban senki sem alkalmazza. Kezdetben kis méretű darabokon kísérleteztünk, teszteltük az anyagokat és a hőmérsékleteket, igaz, sokat hibáztunk, de minden kudarc közelebb vitt ahhoz, hogy egy biztonságos, hatékony módszert dolgozzunk ki. Ennek köszönhetően ma már magabiztosan gyártjuk az alkatrészeket és a szobordarabokat is. Én a stabil stagnálás híve vagyok. A folyamatos fejlődésben hiszek, és arra törekszem, hogy egyre jobb öntvényeket és szolgáltatásokat kínáljunk, egyre gyorsabban, ugyanazon a helyen, ugyanazokkal az emberekkel. Egy olyan csapatot építettünk ki, amely nemcsak dolgozik, hanem tanul és élvezi is, hogy egy izgalmas, innovatív környezet része. Mi azokat a projekteket vállaljuk el, amiket mások lehetetlennek tartanak. Nemrég egy bécsi szobrászművész fordult hozzánk, aki a Művészeti Akadémián a mesterképzésen dolgozott egy lóközpontú szobron, ehhez keresett öntőt. Ausztriában és Németországban mindenki visszautasította vagy irreálisan magas árat kért. Végül az édesapja talált ránk, így elvállaltuk a munkát. A szobor gyönyörűen elkészült, és amikor bemutatta az Akadémián, a professzorok is elismerően tekintettek rá. Ezek a pillanatok, amikor valami lehetetlennek tűnő, mégis megvalósul, a legnagyobb örömmel töltenek el.
Mely alkotásokra a legbüszkébb?
– Számos emlékezetes projektünk bizonyítja munkánk sokszínűségét. Nálunk készült többek között a Székelyudvarhelyen felállított Orbán Balázs-szobor, a nagyváradi Lorántffy Zsuzsanna szobra, Desanka Maksimović ülő szobra, Szarapka Tibor Csúrogon felállított, a Megbékélés nevet viselő szoborcsoportja, a Kosztolányi Dezső egész alakos szobra, ugyancsak Szarapka Tibor alkotása. Ebből az öntödéből került ki Dudás Sándor Magyarkanizsán felállított, Dobó Tihamért és Koncz Istvánt ábrázoló alkotása, meg a szabadkai 44-es parcelláról ellopott Vergődő madár, Bíró Károly szobra és a nagybecskereki Szent István-szobor is. A köztéri szobrok mellett kisméretű szobrokat, érmeket, emléktáblákat is készítettünk, és harangokat is öntünk. Ugyanakkor egy angliai mérőeszköz-gyártó cég számára is rendkívül precíziósan megmunkált mérőágyakat, mérőeszközöket és mérőoszlopokat készítettünk már. Ezek a darabok olyan megmunkált, fölcsiszolt öntvények, amelyek kiállták a legszigorúbb elvárásokat, legyen szó termikus vagy időbeli stabilitásról. Innovációval és technológiai bravúrokkal olyan különleges projekteket is megvalósítunk, mint a szabadkai Elektroremont vállalat számára készült 100 kilowattos bordás motorház, amely 3D-nyomtatás és CNC-modellgyártás révén született meg. A technológiai fejlődés új kapukat nyitott meg számunkra. Nemrégiben hangszerkészítővé is váltunk: alumínium darbukákat készítettünk Nyers Lehel hangszerkészítő számára három méretben. A vékonyfalú öntvények nemcsak gyönyörűek, de hangzásuk is felülmúlja a legdrágább egyiptomi és dubaji modelleket. A 3D-technológia lehetővé tette, hogy gyorsan tökéletes megoldást találjunk a tervezésükhöz, míg korábban akár egy évet is eltarthatott volna ez a folyamat. Számunkra nincs lehetetlen: ha a technológia nem adott, házon belüli fejlesztésekkel teremtünk megoldást. A sikerünk titka a kitartás, az innováció és az, hogy a kudarcok után sem adjuk fel. Az emberi gondolkodás határtalan, és ha elég kreatívan és kitartóan állunk a munkához, bármit megvalósíthatunk. Mindig egy lépéssel a konkurencia előtt kell járnunk, és meg kell találnunk azokat a speciális igényű ügyfeleket, akiket mások nem tudnak kiszolgálni. Így nincs szükség arra, hogy árban versenyezzünk. Szállítunk még egyébként az Európai Unió minden országába, például az építőipar, a tüzeléstechnika vagy a vasút számára gépi- illetve alkatrész-öntvényeket. Vajdaságban régi kombájnok és traktorok működését tesszük lehetővé pótalkatrészeinkkel, bányáknak, malmoknak, acélműveknek is gyártunk alkatrészeket, sőt harangok megalkotása is része a palettánknak. Mindig a kihívásokat keressük, mert nálunk a kudarc csak egy újabb lépcsőfok a siker felé.
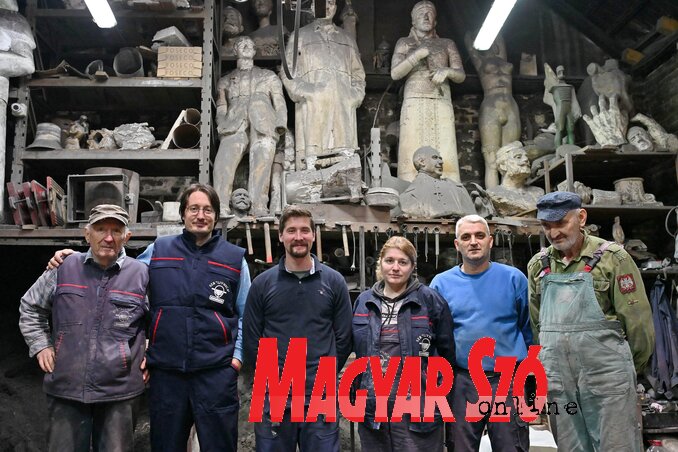
Az öntöde minden alkalmazottja és a vezetőség szinte egy családként tekint egymásra (Fotó: Molnár Edvárd felvétele)
Milyen érzés egy ilyen nagy múltú családi örökséget továbbvinni?
– Különleges érzés. Vajdaságban alig akad háromgenerációs iparos, és ha valaki ugyanazt a mesterséget űzi, amit már a nagyapja is, az ritkaság. Például még mindig gyártjuk a kukoricadaráló bordás kerekét – pontosan ugyanazt, amit 1930-ban is készítettek. Ez nemcsak hasonló, hanem valóban ugyanaz a termék, ami a mai világban szinte elképzelhetetlen, hogy valami ilyen mértékben időtálló legyen. Ez az örökség az, ami miatt 30 évesen úgy döntöttem, hogy hazatérek, és nem egy nagyvárosban leszek egy, a hárommillió fejlesztőmérnök közül, hanem egy teljesen egyedi öntödét építek újra. Bár ez rengeteg stresszel, nehézséggel jár, tudom, hogy maradandót alkotok, és olyan munkát végzek, ami a családi hagyományokat viszi tovább, és időtálló értéket teremt. Az alkotás folyamata a legizgalmasabb számomra. Szinte rendkívüli, hogy a semmiből valami megszületik általunk. Még különlegesebb, amikor harangot öntünk. Ilyenkor gyakran a pap is megjelenik, sőt, volt olyan alkalom, hogy az olvadt bronzot is megszentelte, továbbá hoztak már hívők által gyűjtött ezüstöt is, amit beledobtak az olvadt bronzba.
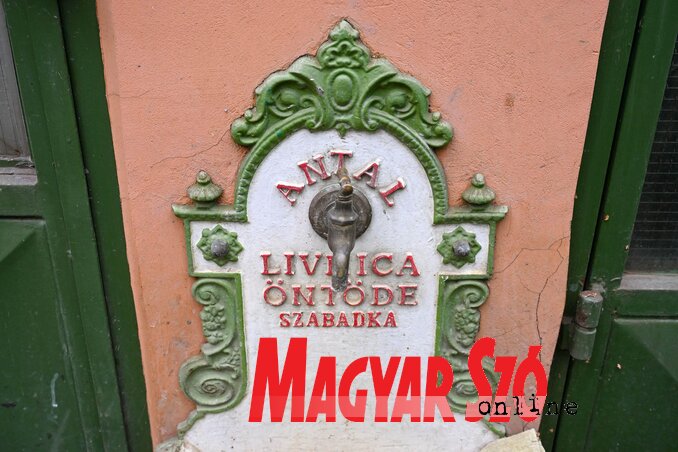
Az Antal-öntöde történelmi jelentőségű, 94 éves múltra tekint vissza (Fotó: Molnár Edvárd felvétele)
Hogyan látja az öntöde jövőjét?
– A legújabb technológiák alkalmazásával. Úgy gondolom, az öntödénk számára a jövőben elengedhetetlen lesz a 3D-fémnyomtatás integrálása. Habár ez egyelőre még megfizethetetlen, néhány éven belül elérheti az átlag ipari felhasználói árszinteket, és áttörést hozhat a régióban. Ez a technológia jelentősen lerövidíti az iterációs ciklusokat, így akár egy hét alatt öt változtatást is kipróbálhatunk egy prototípuson, míg a hagyományos öntödékben hetek, hónapok szükségesek ehhez. A fejlődés megállítása lehetetlenné tenné, hogy lépést tartsunk az új generációs igényekkel. Csak úgy tudunk megfelelni a terméktervezők és gépészmérnökök elvárásainak, ha folyamatosan alkalmazzuk az új technológiai fejlesztéseket.
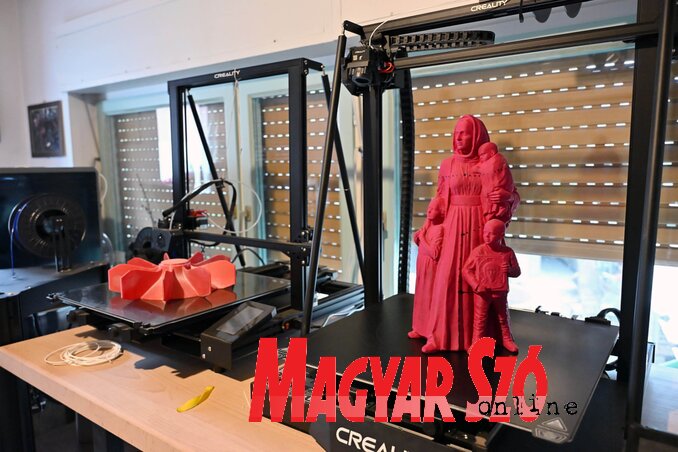
Egy 3D-s nyomtatóval készült alkotás (Fotó: Molnár Edvárd felvétele)

Nyitókép: Az olvasztótégelyben izzó állapotban van az olvadt fém, amelyet később formákba öntenek (Fotó: Molnár Edvárd felvétele)